【壓縮機網】3月12日,霍尼韋爾UOP宣布,浙江石油化工有限公司將在其位于浙江省舟山市的煉化一體化二期項目中安裝四套霍尼韋爾UOP Polybed變壓吸附 (PSA) 裝置,以供應高純度氫氣。
浙江石化舟山煉化一體化項目的一期和二期項目均已采用了霍尼韋爾UOP的工藝技術授權、工藝包設計和催化劑等服務和產品。舟山項目建成后有望成為中國大型的原油制化學品一體化化項目,也將躋身全球大型同類項目之列,主要生產制造聚酯、薄膜和纖維以及燃料的石化產品。
霍尼韋爾特性材料和技術集團副總裁兼亞太區(qū)總經理、霍尼韋爾UOP中國區(qū)副總裁兼總經理劉茂樹表示:“霍尼韋爾UOP的PSA技術具備出色的競爭力和可靠的高純度氫氣生產能力,因此備受中國石化煉廠的青睞。高純度氫氣是確保高集成煉化裝置高效運行的關鍵要素,所有轉化技術都依賴于它。”
浙石化與霍尼韋爾合作大事記
2017年2月
霍尼韋爾UOP為舟山煉化一體化項目一期工程提供多項技術,包括氫氣處理、重油催化裂化、催化重整、加氫裂化、重油改質,以及以LD Parex為核心的芳烴聯(lián)合技術,用于生產聚酯、薄膜、纖維等數(shù)以百萬種產品的原料。霍尼韋爾過程控制部也將為該項目提供先進的自動化控制技術Experion過程知識系統(tǒng)(PKS)。
2017年5月
雙方擴大合作,霍尼韋爾UOP為該煉化一體化項目提供四套Polybed變壓吸附 (PSA) 裝置,用來生產高純度氫氣。同時,該項目還采用霍尼韋爾過程控制部先進的Experion分布式控制系統(tǒng),用于控制PSA裝置生產。
四套Polybed變壓吸附(PSA) 裝置,用來生產高純度氫氣。
霍尼韋爾過程控制部先進的Experion分布式控制系統(tǒng),該系統(tǒng)集成了霍尼韋爾先進的C300控制器,用于控制PSA裝置生產。
2019年1月
霍尼韋爾UOP宣布為該煉化一體化二期項目提供一系列工藝技術,目標是將裝置的芳烴產能翻一番,達到每年約1,200萬噸。包括繼續(xù)提供一系列工藝技術授權、工藝包設計、關鍵設備,以及先進的催化劑和吸附劑。此外,霍尼韋爾Experion過程知識系統(tǒng)(PKS)也為該一體化項目提供過程控制和自動化系統(tǒng)。
2019年11月
雙方簽訂《智能互聯(lián)工廠建設合作諒解備忘錄》,致力于打造更為現(xiàn)代和智能的新一代互聯(lián)工廠。并同時宣布在該煉化一體化二期項目中采用霍尼韋爾UOP的一系列先進技術,包括工藝技術、催化劑和關鍵設備。
關于霍尼韋爾UOP PolybedPSA技術
PolybedPSA系統(tǒng)為撬裝模塊化裝置,集硬件設備、吸附劑、控制系統(tǒng)和嵌入式工藝技術于一體,可實現(xiàn)快速高效的安裝,從而有效降低成本,縮短建設周期。
PSA工藝采用UOP的專利吸附劑,可在高壓下除去含氫氣體中的雜質,回收氫氣并提純到99.9%以上,從而滿足精煉需求。除了從重整爐和煉油廢氣中回收和提純氫氣外,PolybedPSA系統(tǒng)還能利用其它氣體(如乙烯廢氣、甲醇廢氣和部分氧化合成氣)來生產氫氣。
自PSA技術1966年問世以來,UOP通過采用新一代吸附劑,強化循環(huán)配置,改良工藝和裝置設計,部署可靠的控制系統(tǒng)和設備,持續(xù)改進PolybedPSA技術。目前,霍尼韋爾UOP已在全球70多個國家和地區(qū)成功安裝了1100多套PolybedPSA裝置。作為一項成熟的技術,PolybedPSA在全球范圍內擁有數(shù)十套大型裝置的成功案例。
關于舟山一體化項目
該項目是世界上大型的原油制化學品一體化項目之一,項目建成后,原油到石化產品的轉化率將高于50%,不僅能助力中國實現(xiàn)對二甲苯自給自足的目標,同時還能成為丙烯和其他產品的新生產基地。
包括兩大石化綜合體:兩個年產能總計為800萬噸的霍尼韋爾UOP VGO Unicracking裝置,兩個總年產能為700萬噸的柴油加氫裂化裝置。此外,這兩大石化綜合體還擁有一個采用RCD union fining和RFCC工藝的催化裂化聯(lián)合裝置,年產能達500萬噸,四個年產能總計為1520萬噸的CCR Platforming重整裝置,一個年產能40萬噸的Butamer裝置,四個總年產能880萬噸的LD-Parex技術芳烴聯(lián)合裝置,以及一個年產能為51萬噸的C3 Oleflex丙烷脫氫裝置。
來源:氣體分離
浙江石化舟山煉化一體化項目的一期和二期項目均已采用了霍尼韋爾UOP的工藝技術授權、工藝包設計和催化劑等服務和產品。舟山項目建成后有望成為中國大型的原油制化學品一體化化項目,也將躋身全球大型同類項目之列,主要生產制造聚酯、薄膜和纖維以及燃料的石化產品。
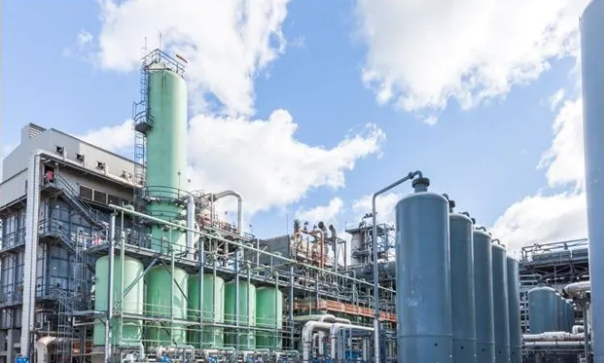
霍尼韋爾特性材料和技術集團副總裁兼亞太區(qū)總經理、霍尼韋爾UOP中國區(qū)副總裁兼總經理劉茂樹表示:“霍尼韋爾UOP的PSA技術具備出色的競爭力和可靠的高純度氫氣生產能力,因此備受中國石化煉廠的青睞。高純度氫氣是確保高集成煉化裝置高效運行的關鍵要素,所有轉化技術都依賴于它。”
浙石化與霍尼韋爾合作大事記
2017年2月
霍尼韋爾UOP為舟山煉化一體化項目一期工程提供多項技術,包括氫氣處理、重油催化裂化、催化重整、加氫裂化、重油改質,以及以LD Parex為核心的芳烴聯(lián)合技術,用于生產聚酯、薄膜、纖維等數(shù)以百萬種產品的原料。霍尼韋爾過程控制部也將為該項目提供先進的自動化控制技術Experion過程知識系統(tǒng)(PKS)。
2017年5月
雙方擴大合作,霍尼韋爾UOP為該煉化一體化項目提供四套Polybed變壓吸附 (PSA) 裝置,用來生產高純度氫氣。同時,該項目還采用霍尼韋爾過程控制部先進的Experion分布式控制系統(tǒng),用于控制PSA裝置生產。
四套Polybed變壓吸附(PSA) 裝置,用來生產高純度氫氣。
霍尼韋爾過程控制部先進的Experion分布式控制系統(tǒng),該系統(tǒng)集成了霍尼韋爾先進的C300控制器,用于控制PSA裝置生產。
2019年1月
霍尼韋爾UOP宣布為該煉化一體化二期項目提供一系列工藝技術,目標是將裝置的芳烴產能翻一番,達到每年約1,200萬噸。包括繼續(xù)提供一系列工藝技術授權、工藝包設計、關鍵設備,以及先進的催化劑和吸附劑。此外,霍尼韋爾Experion過程知識系統(tǒng)(PKS)也為該一體化項目提供過程控制和自動化系統(tǒng)。
2019年11月
雙方簽訂《智能互聯(lián)工廠建設合作諒解備忘錄》,致力于打造更為現(xiàn)代和智能的新一代互聯(lián)工廠。并同時宣布在該煉化一體化二期項目中采用霍尼韋爾UOP的一系列先進技術,包括工藝技術、催化劑和關鍵設備。
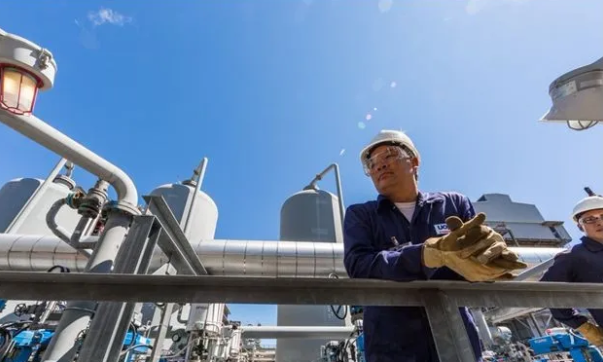
關于霍尼韋爾UOP PolybedPSA技術
PolybedPSA系統(tǒng)為撬裝模塊化裝置,集硬件設備、吸附劑、控制系統(tǒng)和嵌入式工藝技術于一體,可實現(xiàn)快速高效的安裝,從而有效降低成本,縮短建設周期。
PSA工藝采用UOP的專利吸附劑,可在高壓下除去含氫氣體中的雜質,回收氫氣并提純到99.9%以上,從而滿足精煉需求。除了從重整爐和煉油廢氣中回收和提純氫氣外,PolybedPSA系統(tǒng)還能利用其它氣體(如乙烯廢氣、甲醇廢氣和部分氧化合成氣)來生產氫氣。
自PSA技術1966年問世以來,UOP通過采用新一代吸附劑,強化循環(huán)配置,改良工藝和裝置設計,部署可靠的控制系統(tǒng)和設備,持續(xù)改進PolybedPSA技術。目前,霍尼韋爾UOP已在全球70多個國家和地區(qū)成功安裝了1100多套PolybedPSA裝置。作為一項成熟的技術,PolybedPSA在全球范圍內擁有數(shù)十套大型裝置的成功案例。
關于舟山一體化項目
該項目是世界上大型的原油制化學品一體化項目之一,項目建成后,原油到石化產品的轉化率將高于50%,不僅能助力中國實現(xiàn)對二甲苯自給自足的目標,同時還能成為丙烯和其他產品的新生產基地。
包括兩大石化綜合體:兩個年產能總計為800萬噸的霍尼韋爾UOP VGO Unicracking裝置,兩個總年產能為700萬噸的柴油加氫裂化裝置。此外,這兩大石化綜合體還擁有一個采用RCD union fining和RFCC工藝的催化裂化聯(lián)合裝置,年產能達500萬噸,四個年產能總計為1520萬噸的CCR Platforming重整裝置,一個年產能40萬噸的Butamer裝置,四個總年產能880萬噸的LD-Parex技術芳烴聯(lián)合裝置,以及一個年產能為51萬噸的C3 Oleflex丙烷脫氫裝置。
來源:氣體分離
網友評論
條評論
最新評論