Atlas Copco introduces SmartLink 2.0 to provide air users with easily actionable IoT-driven insights
May 18, 2020
Atlas Copco has released a new version of its SmartLink remote monitoring system ? SmartLink 2.0 – that gives air users complete, easily actionable IoT- driven insights, not just data, and early warnings from their compressed air system.
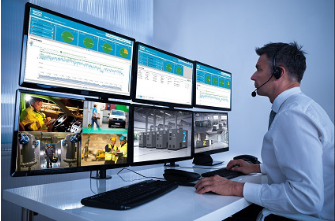
Knowing the status of compressed air equipment at all times is the surest way to spot any developing problems, uncover potential energy savings and achieve maximum uptime for compressors and production lines. With SmartLink 2.0, new, simple dashboards provide an enhanced Human Machine Interface (HMI) allowing users much more interaction with their air compressor systems and presenting information on 'events,' e.g. potential failure/pressure drops / required maintenance, in a way that makes them quicker to action.
With 24/7 connectivity via the integrated, easily installed, wireless Smartbox, SmartLink 2.0 provides a tailored compressor monitoring service program that
gathers, compares and analyses data on the fly. Information from all installations comes to one server enabling users to view parameters such as uptime, energy efficiency, equipment health, recommendations, and service timeline on their screens or mobile devices.
In keeping with Atlas Copco’s original SmartLink 1.0 concept, compressor system users can choose from 3 levels of remote data monitoring to determine the amount of interactive information they receive. These are SmartLink Service, SmartLink Uptime and SmartLink Energy.
With SmartLink Service, users have complete insight into current and future maintenance needs of the compressor ? a guide into necessary actions to maintain compressors correctly and avoid any risk of production interruption.
The Service dashboard displays active and historic events plus maintenance requirements. The Service timeline and reports indicate service status, planned and executed service jobs and field reports of every action performed by Atlas Copco engineers. Machine panels list all on-site equipment and include an individual machine overview page.
The next level is SmartLink Uptime. This includes all the Service package features but in addition, provides event warning notification. The Uptime dashboard indicates availability details of all connected equipment within a compressed air installation. Users are alerted via SMS mail or push notifications so as to be on top of machine events or self-defined warnings. The dashboard details indicate equipment health status that is based on maintenance, machine condition, and running condition checks.
With the SmartLink Energy level, which embraces the benefits of both the Service and Uptime programmes, the interactive dashboard provides information on energy and performance KPI. It also reveals insights into energy consumption and evolution as well as energy efficiency and achieved savings, machine usage and productive times. A graphic display of all measured data is available for trending and data export, and users can download or schedule customisable reports for performance analysis.
An important, optional addition to the SmartLink suite is SmartLink SPM which allows users to analyse the condition of main rotating components, compensate for speed variations, and substitute unplanned downtime with planned overhaul. It represents the means to maximise operational life without incurring risks. The dashboard provides condition conclusions per machine and its components.
Furthermore, the SPM trend graphs present an easy to read condition evolution of each monitored component. Recommendations come in the form of pro-active advice when the condition of a component needs to be verified.
In summary, Atlas Copco’s SmartLink 2.0 offers compressor users insights derived from actionable dashboards, customised views, pro-active advice and alerts. It enables interaction that is fast and mobile, and an intelligent assessment of a compressed air system’s performance that avoids the costs of unplanned downtime and repair.